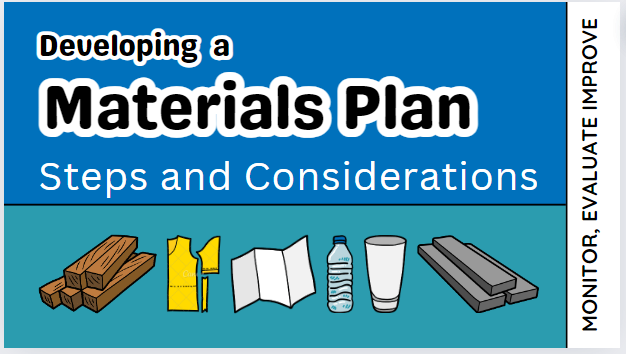
Material management is a critical component of any business that involves the sourcing, production, and delivery of goods. An effective material management plan ensures that the right materials are available at the right time, in the right quantity, and at the right cost. This process not only helps in reducing waste and costs but also improves the efficiency of the entire supply chain. In this blog, we’ll explore the key steps and considerations involved in developing a robust material management plan.
1. Define Objectives and Scope
The first step in developing a material management plan is to clearly define the objectives and scope of the plan. Objectives should align with the overall business goals and may include reducing costs, improving production efficiency, enhancing quality control, or achieving sustainability targets. Defining the scope involves determining which materials, processes, and departments will be covered by the plan. This foundational step helps in setting clear expectations and provides a framework for the rest of the planning process.
2. Conduct a Material Needs Assessment
A thorough material needs assessment is essential for understanding the types and quantities of materials required. This involves analyzing past data, forecasting future demand, and considering factors such as seasonal variations, market trends, and production schedules. The assessment should also account for safety stock levels to mitigate the risk of shortages. Tools like Material Requirements Planning (MRP) software can assist in accurately determining material needs and optimizing inventory levels.
3. Select and Evaluate Suppliers
Choosing the right suppliers is crucial for ensuring a reliable supply of quality materials. The selection process should include evaluating potential suppliers based on criteria such as price, quality, reliability, and delivery times. Building strong relationships with suppliers can lead to better terms, improved communication, and more consistent material quality. It’s also important to have a backup plan in case of supplier disruptions, which could include maintaining relationships with multiple suppliers or having contingency contracts in place.
4. Develop Procurement and Inventory Policies
Once suppliers are selected, the next step is to establish procurement and inventory policies. These policies should outline the procedures for ordering materials, including order quantities, lead times, and reordering points. The policies should also define inventory management practices, such as First-In-First-Out (FIFO) or Just-In-Time (JIT) inventory systems. Effective inventory management helps in minimizing carrying costs and reducing the risk of obsolescence.
5. Implement Quality Control Measures
Quality control is a vital aspect of material management, as the quality of materials directly impacts the quality of the final product. The plan should include procedures for inspecting materials upon receipt and monitoring supplier performance. Regular audits and quality checks can help in identifying and addressing any issues promptly. Additionally, establishing clear quality standards and communicating them to suppliers ensures that expectations are met consistently.
6. Establish Communication and Coordination Protocols
Effective communication and coordination are essential for the smooth execution of a material management plan. This involves establishing protocols for sharing information between different departments, such as procurement, production, and logistics. Regular meetings and updates can help in keeping everyone informed about material availability, potential issues, and upcoming changes. Utilizing digital tools and software can facilitate real-time communication and improve overall coordination.
7. Implement Technology and Automation
Leveraging technology and automation can greatly enhance the efficiency of material management processes. Enterprise Resource Planning (ERP) systems, for example, can integrate various functions such as procurement, inventory management, and production planning into a single platform. Automated systems can help in tracking inventory levels, generating purchase orders, and managing supplier relationships. Additionally, technologies like the Internet of Things (IoT) can provide real-time data on material usage and availability, enabling more accurate decision-making.
8. Monitor, Evaluate, and Improve
The final step in developing a material management plan is to establish a system for monitoring and evaluating the plan’s effectiveness. Key Performance Indicators (KPIs) such as inventory turnover, order accuracy, and supplier lead times can provide valuable insights into the plan’s performance. Regular reviews and audits should be conducted to identify areas for improvement and make necessary adjustments. Continuous improvement is key to maintaining an efficient and cost-effective material management system.
Considerations for a Successful Material Management Plan
While developing a material management plan, several considerations should be kept in mind:
Flexibility and Adaptability
The plan should be flexible enough to adapt to changing market conditions, customer demands, and technological advancements.
Risk Management
Identifying potential risks, such as supply chain disruptions or material shortages, and developing contingency plans can help mitigate these risks.
Sustainability
Incorporating sustainable practices, such as sourcing eco-friendly materials and reducing waste, can enhance the plan’s long-term viability and align with corporate social responsibility goals.
Training and Development
Ensuring that employees are well-trained in material management processes and technologies is crucial for the successful implementation of the plan.
How MITSDE Provides the Best Skills and Training to Develop a Material Management Plan
MIT School of Distance Education (MITSDE) offers comprehensive courses in Material Management designed to equip students with the essential skills and knowledge needed to excel in this field. The curriculum is carefully crafted to cover all aspects of material management, including procurement, inventory control, quality assurance, and supplier relationship management. MITSDE’s programs are delivered by industry experts and experienced faculty who provide practical insights and real-world examples.
Additionally, the use of advanced technologies such as Enterprise Resource Planning (ERP) systems and Material Requirements Planning (MRP) software is emphasized, allowing students to gain hands-on experience with the tools used in the industry. Through a combination of theoretical knowledge and practical assignments, MITSDE prepares students to develop effective material management plans that are both efficient and adaptable to changing market conditions. The flexible online learning platform and continuous support from faculty ensure that students can balance their studies with professional and personal commitments, making MITSDE an ideal choice for working professionals looking to advance their careers in material management.
Conclusion
Developing an effective material management plan involves careful planning, thorough analysis, and continuous improvement. By defining clear objectives, conducting a material needs assessment, selecting reliable suppliers, and implementing quality control measures, businesses can optimize their material management processes. Leveraging technology and maintaining flexibility further enhance the plan’s effectiveness. With a well-crafted material management plan, businesses can achieve cost savings, improve efficiency, and support overall business success.